Showing 100 results for Alloy
M. S. Kaiser,
Volume 11, Issue 4 (12-2014)
Abstract
The evaluation of texture as a function of recrystallization has been characterized for directly cold rolled Al-6Mg, Al-6Mg-0.4Sc and Al-6Mg-0.4Sc-0.2Zr alloys. Samples were annealed isothermally at 400 °C for 1 to 240 minutes to allow recrystallization. Recrystallization kinetics of the alloys is analyzed from the micro-hardness variation. Isothermally annealed samples of aluminum alloys were also studied using JMAK type analysis to see if there exists any correlation between the methods. Recrystallization fraction behavior between two methods the scandium added alloys show the higher variation due to precipitation hardening and higher recrystallization behavior. The scandium and zirconium as a combined shows the more variation due to formation of Al3(Sc, Zr) precipitate. From the microstructure it is also observed that the base Al-Mg alloy attained almost fully re-crystallized state after annealing at 400 °C for 60 minutes
M. Abbas, S. Nisar, A. Shah, F. Imtiaz Khan,
Volume 12, Issue 2 (6-2015)
Abstract
Aluminium base alloy (Al-Cu-Si) was reinforced with silicon carbide (SiC) particles, in various percentage
compositions from 0-20 wt%. Silicon carbide particle size of 20µm was selected. The molten slurry of SiC reinforced
base aluminium metal was casted through green and dry sand casting methods and solidification process was carried
out under ambient conditions. A selected population of total casted samples were subjected to T6 heat treatment
process, followed by evaluation of mechanical properties of hardness, tensile strength and impact loading. The micro
sized SiC particles were preheated up to 300C prior pouring into the melted metal, for subsequent removal of residual
gases and moisture content. A continuous manual stirring method was used for homogenous distribution of reinforced
particle in molten slurry. The experimental results revealed that the highest parameters of hardness, impact energy and
tensile strength were achieved in the T6 heat treated specimens having highest percentage composition (20%) of
Silicon Carbide (SiC) particles
H. Nazemi, M. Ehteshamzadeh,
Volume 12, Issue 3 (9-2015)
Abstract
Compression springs were prepared from Cr-Si high strength spring steel and coated with pure Zn and ZnNi by electroplating process. The effect of baking after electroplating as well as applying an electroless nickel
interlayer on the fatigue and fatigue corrosion of the springs was investigated. The results were analyzed using weibull
statistical model. A considerable improvement (8%) in fatigue life of the electroplated springs with Zn-Ni was observed
in the presence of Ni interlayer. In addition, baking of these electroplated springs improved fatigue life by 4%. The
fatigue life under salt spraying conditions, however, has demonstrated remarkable reduction by 40%, 34% and 30%
for Zn-Ni plating, backed and unbaked Zn-Ni plating containing Ni interlayer, respectively
M. Amuei, M. Emamy, R. Khorshidi, A. Akrami,
Volume 12, Issue 3 (9-2015)
Abstract
In this study, Al2014 alloy refined with Al-5%Ti-1%B master alloy was prepared by strain-induced melt
activated (SIMA) process. The main variables of the SIMA process were cold working, holding time and temperature in
semi-solid state. Cold working was applied on specimens by upsetting technique to achieve 10%, 20% and 30% height
reduction. Cold worked specimens were heat treated in semi-solid state at 585 °C, 595 °C, 605 °C, 615 °C, 625 °C and
635 °C and were kept in these temperatures for different times (20 and 30 min). Observations through optical and
scanning electron microscopy were used to study the microstructural evaluation. The results revealed that fine and
globular microstructures are obtained by applying 30 % height reduction percentage and heat treating in 625 °C for
30 min. Comparison between refined and unrefined Al2014 alloy after applying SIMA process showed that Al-5%Ti-1%B master alloy has no significant effect on average globule size but makes the final structure more globular.
A. Abbasian, M. Kashefi, E. Ahmadzade-Beiraki,
Volume 12, Issue 3 (9-2015)
Abstract
Precipitation hardening is the most common method in the strengthening of aluminium alloys. This method
relies on the decrease of solid solubility with temperature reduction to produce fine precipitations which impede the
movement of dislocations. The quality control of aluminium alloy specimens is an important concern of engineers.
Among different methods, non-destructive techniques are the fastest, cheapest and able to be used for all of parts in a
production line. To assess the ability of eddy current as a non-destructive method in the evaluation of precipitation
hardening of aluminium alloys, 7075 aluminium alloy specimens were solution treated at 480°C for 1 hr. and followed
by water quenching. Afterwards, the specimens were aged at different temperatures of 200, 170, 140, 110 and 80°C for
8 hr. Eddy current measurements was conducted on the aged specimens. Hardness measurement and tensile test were
employed to investigate the mechanical properties. It was demonstrated that eddy current is effectively able to separate
the specimens with different aging degree due to the change of electrical conductivity during aging process
M. Ershadi Khameneh, H. Shahverdi, M. M. Hadavi,
Volume 12, Issue 4 (12-2015)
Abstract
Creep age forming (CAF) is one of the novel methods in aerospace industry that has been used to manufacture components of panels with improved mechanical properties and reduced fabrication cost. CAF is a combined age-hardening and stress-relaxation that are responsible for strengthening and forming, respectively. This paper deals with the experimental investigations of mechanical and springback properties of Al-Zn-Mg Al alloy in creep forming process. Creep forming experiments have been performed at temperatures of 120◦C and 180◦C for 6–72 h. Results indicated that yield stress and hardness of creep age formed specimens increased with increasing forming time and temperature, simultaneously induced deflection by stress-relaxation increased. Incorporating spring back and mechanical properties, it can be found that the appropriate forming cycle was 180 ◦C/24 h among all forming conditions. CAF Time increase to a certain extent increased mechanical properties. This can be attributed to presence of stress in CAF that causes the precipitates be finer because of creation more nucleation sites. Therefor the growth of precipitates, takes place at long time and postpones the decreasing of the yield stress
M. Dehnavi, M. Haddad-Sabzevar, M.h. Avazkonandeh-Gharavol, H. Vafaeenezhad,
Volume 12, Issue 4 (12-2015)
Abstract
Microsegregation is one of the most important phenomena occurs during solidification. It usually results in formation of some unexpected second phases which generally affect the mechanical properties and specially reduce the workability of casting products. The aim of this research is to study the effect of cooling rate and grain refinement on the microsegregation in Al-4.8 wt.% Cu. For this purpose two series of experiments were designed. In the first set of experiments, the alloy was melted and cooled in three different rates, i.e. 0.04, 0.42, and 1.08 K/s in a DTA furnace. In the second series of experiments, the effect of grain refinement on the microsegregation at a constant cooling rate of 0.19 K/s was investigated. Al-5Ti-1B master alloy was used as grain refiner. Results showed that by increasing the cooling rate the amount of non-equilibrium eutectic phase increases from 5.1 to 7.4 wt.%, and the minimum concentration of solute element in primary phase decreases from 1.51 to 1.05 wt.% Cu. By grain refinement of the alloy, the amount of non-equilibrium eutectic phase decreases from 5.5 to 4.7 wt.%, and the minimum concentration of solute element in the primary phase increases from 0.98 to 1.07 wt.% Cu. So it is concluded that increasing cooling rate in the range of 0.04 to 1.08 K/s, increases and grain refinement reduces the microsegregation
E. Barati, Kh. Farmanesh,
Volume 12, Issue 4 (12-2015)
Abstract
The purpose of this research is to achieve the optimal parameters for producing forged aluminium alloy 7075 aircraft door bracket by using finite element modelling (FEM) with commercial DEFORM-3D V6.1 and physical simulations with plasticine and Plexiglas dies. Also, forging speed has been examined as the main factor for controlling to produce a part without any defects. The results of Physical Simulation showed that the flow pattern has good agreement with the results of FEM that based on the use of hydraulic presses with initial billet and dies temperatures 410 and 400 ° C, respectively, and different forging speeds 5, 10 and 15 mm/sec. Distribution of effective strain rate, effective strain, effective stress, temperature , forging force and dies wear showed improvement the results in forging speed of 5 mm/sec. Processing map of Aluminium alloy 7075 also checked out at constant strain 0.5, indicated that the specified area of the forged part is located in a safe area. Forging force in optimized forging speed 5 mm/sec showed that the forging process using a 1000-ton press can be done easily
M. Maddah, M. Rajabi, S. M. Rabiee,
Volume 12, Issue 4 (12-2015)
Abstract
In this study, the composite material with composition of MgH2-5 wt% SiC has been prepared by co-milling of MgH2 with SiC powder. The effect of milling time and additive on MgH2 structure, i.e. crystallite size, lattice strain, particle size and specific surface area, and also hydrogen desorption properties of obtained composite was evaluated by thermal analyzer method and compared with pure un-milled MgH2. The phase constituents and grain size of powder were characterized by X-ray diffractometry method. It has been shown that addition of 5 wt% SiC to MgH2 and mechanical alloying up to 30 h formed a nanocrystalline composite with the average crystallite size of 12 nm, average particle size of 0.5 µm and specific surface area of 10 m2/g. On the other hand, SiC can help to break up particles and reduce the particle size. As a consequence, the desorption temperature of composite material milled for 30 h has decreased from 435 °C to 361 °C.
M.h. Avazkonandeh-Gharavo, M. . Haddad-Sabzevar, H. Fredriksson,
Volume 13, Issue 2 (6-2016)
Abstract
Because the partition coefficient is one of the most important parameters affecting microsegregation, the aim of this research is to experimentally analyse the partition coefficient in Al-Mg alloys. In order to experimentally measure the partition coefficient, a series of quenching experiments during solidification were carried out. For this purpose binary Al-Mg alloys containing 6.7 and 10.2 wt-% Mg were melted and solidified in a DTA furnace capable of quenching samples during solidification. Cooling rates of 0.5 and 5 K/min were used and samples were quenched from predetermined temperatures during solidification. The fractions and compositions of the phases were measured by quantitative metallography and SEM/EDX analyses, respectively. These results were used to measure the experimental partition coefficients. The resultant partition coefficients were used to model the concentration profile in the primary phase and the results were compared with equilibrium calculations and experimental profiles. The results of calculations based on the experimental partition coefficients show better consistency with experimental concentration profiles than the equilibrium calculations.
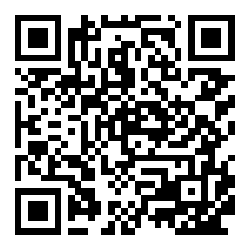
S. Yazdani, S. Javadpour, Sh. Mehdizadeh Naderi, M. Javidi,
Volume 13, Issue 2 (6-2016)
Abstract
The inherent reactivity of the Al–Cu alloys is such that their use for structural, marine, and aerospace components and structures would not be possible without prior application of a corrosion resistance system. Historically these corrosion resistance coatings were based on the use of chemicals containing Cr (VI) compounds. Silane coatings are of increasing interest in industry due to their potential application for the replacement of current toxic hexavalent chromate based treatments. In this study, hydrophobic coating sol was prepared with methyltriethoxysilane (MTES), methanol (MeOH), and water (as 7M NH4OH) at a molar ratio of 1:25:4.31 respectively. The coatings were applied by a dip-technique to 2024-T3 Al alloy, and subsequently cured at room temperature and there after heat treated in an oven at 150°C. The anticorrosion properties of the coatings within 3.5 wt% NaCl solution were studied by Tafel polarization technique. The sol–gel coating exhibited good anticorrosion properties providing an adherent protection film on the Al 2024-T3 substrate. The surface properties were characterized by water contact angle measurement, scanning electron microscopy (SEM), and the composition was studied by Fourier transform infrared spectroscopy (FTIR).
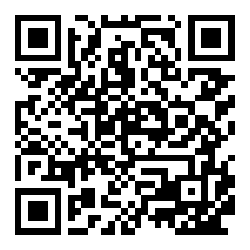
Z. Sadeghian, R. Dezfulizadeh,
Volume 13, Issue 2 (6-2016)
Abstract
In situ Al2024- Mg2Si composite was fabricated by spark plasma sintering (SPS) of reactive powder. Reactive powder was obtained from mechanical alloying (MA) of elemental powders. Clad layers of in situ composite were fabricated on Al substrates by spark plasma sintering (SPS). Structural evolution during MA process and after SPS was investigated by X-ray diffractometery (XRD). Scanning electron microscopy (SEM) was utilized to study the microstructure of sintered samples. Hardness and tensile behavior of sintered samples were investigated. The results showed that SPS of mechanically alloyed unreacted powder can result in the in situ formation of Mg2Si and Mg2Al3 within the Al matrix. SPSed clad layer showed a sound and clear interface to the Al substrate with a hardness of about 140 HV. Sintered in situ composite exhibited a tensile strength of 288 MPa.
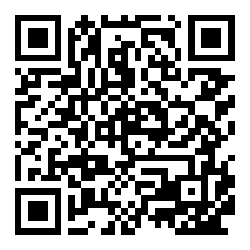
. S. Khani, . M. T. Salehi, . H. R. Samim, Prof. M. R. Aboutalebi, . H. Palkowski,
Volume 13, Issue 3 (9-2016)
Abstract
The evolution of microstructure and mechanical properties of a magnesium cast alloy (AZ31) processed by equal channel angular pressing (ECAP) at two different temperatures were investigated. The as-cast alloy with an average grain size of 360 was significantly refined to about 5 after four ECAP passes at 543 K. Grain refinement was achieved through dynamic recrystallization (DRX) during the ECAP process in which the formation of necklace-type structure and bulging of original grain boundaries would be the main mechanisms. ECAP processing at lower temperature resulted in finer recrystallized grains and also a more homogenous microstructure. The mechanical behavior was investigated at room temperature by tensile tests. The obtained results showed that the ECAP processing can basically improve both strength and ductility of the cast alloy. However, the lower working temperature led to higher yield and ultimate strength of the alloy.
E. Gharibshahiyan, A. Honarbakhsh Raouf,
Volume 13, Issue 4 (12-2016)
Abstract
Friction welding is widely used in various industries. In friction welding, heat is generated by conversion of mechanical energy into thermal energy at the interface the work pieces during pin rotation under pressure. A three-dimensional thermo mechanical simulation of friction stir welding (FSW) processes is carried out for Aluminium Alloys of 6061and 7050 where the simulation results are compared directly with the measured temperature histories during FSW after process. The objective of the present work is to study and predict the heat transient generated in alloy aluminium plate welded by FSW method. A three dimensional model was developed by LS-Dyna software and heat cycles have been proposed during the welding of aluminium alloys 6061 and 7050. In this research, the simulations were carried out with linear velocity in the range of 140 to 225 mm/min and pin rotational speeds of 390 and 500 rpm. Increase in pin rotational speed, from 390 to 500 rpm, resulted in greater temperatures which translated to rise of recorded temperature of top and bottom of the specimens. This is in turn to a wider HAZ. In addition, it was observed that raising the linear velocity had an opposite effect. Finally, results of experimental and numerical data were correlated and validated
M. Shahmiri,
Volume 13, Issue 4 (12-2016)
Abstract
Over the last few decades, there have been many mechanisms proposed to describe the formation of the non-dendritic microstructures during Semisolid Metal (SSM) processing; including dendrite fragmentation, spherical growth, cellular growth and recalescence. Dendrite fragmentation is the most popular mechanism of all these hypotheses. It is the purpose of the present article to examine the morphological evolution of the non-dendritic microstructures, based on models proposed by Flemings, Vogel, Cantor, and Doherty during SSM processing of the Al-Si (A356) alloy. Based on new microstructural evidences, including (1) - plastic deformation at the side arms by slip lines formation as a result of the thermal fatigue mechanism, (2) - crack formation at the root of the side arms and (3) – the interaction of a rapidly sheared hot viscous medium with these regions, i.e. erosion; it propose and hereby discuss a new mechanism called "fatigue –erosion", for dendrites fragmentation of the experimental alloy. Optical and Scanning Electron Microscopy (SEM) with EBSD and EDS, TEM, and AFM was used for the microstructural characterizations.
M. Paidpilli, K. Verma, R. Pandey, A. Upadhyaya,
Volume 14, Issue 1 (3-2017)
Abstract
In the present work, one batch of prealloyed 6061Al powder was processed by mixing and another one was ball milled with varying amount of lead content (0-15 vol. %). These powders were compacted at 300MPa and sintered at 590˚C under N2. The instrumented hardness and the young’s modulus of as-sintered 6061Al-Pb alloys were examined as a function of lead content and processing route. The wear test under dry sliding condition has been performed at varying loads (10-40 N) using pin-on-disc tribometer. The microstructure and worn surfaces have been investigated using SEM to evaluate the change in topographical features due to mechanical alloying and lead content. The mechanically alloyed materials showed improved wear characteristics as compared to as-mixed counterpart alloys. Delamination of 6061Al-Pb alloys decreases up to an optimum lead composition in both as-mixed and ball-milled 6061Al-Pb alloys. The results indicated minimum wear rate for as-mixed and ball-milled 6061Al alloy at 5 and 10 vol. % Pb, respectively.
A. Ataei, M. Jalaly, M. Tamizifar,
Volume 14, Issue 1 (3-2017)
Abstract
The boronizing of a tungsten heavy alloy containing Ni and Fe as the major alloying elements were performed in the present study to increase its surface hardening. Pack cementation method was employed as a well-known, successful solid-state process for boronizing. The coating treatment was accomplished at different temperatures of 1000, 1050 and 1100°C for 6 and 9 hours. The formation of tungsten boride phase was confirmed, although a silicide layer covered the surface of the specimen as the outer layer. The mechanism of the formation of a multilayered surface was explained. The maximum thickness of reaction zone and surface hardness achieved in the current work were 300 µm and 2470 HV, respectively.
H. Torkamani, H. Rashvand, Sh. Raygan, J. Rassizadehghani, Y. Palizdar, C. Garcia Mateo, D. San Martin,
Volume 14, Issue 3 (9-2017)
Abstract
In industry, the cost of production is an important factor and it is preferred to use conventional and low cost procedures for producing the parts. Heat treatment cycles and alloying additions are the key factors affecting the microstructure and mechanical properties of the cast steels. In this study an attempt was made to evaluate the influence of minor Mo addition on the microstructure and mechanical properties of conventionally heat treated cast micro-alloyed steels. The results of Jominy and dilatometry tests and also microstructural examinations revealed that Mo could effectively increase the hardenability of the investigated steel and change the microstructure features of the air-cooled samples. Acicular microstructure was the consequence of increasing the hardenability in Mo-added steel. Besides, it was found that Mo could greatly affect the isothermal bainitic transformation and higher fraction of martensite after cooling (from isothermal temperature) was due to the Mo addition. The results of impact test indicated that the microstructure obtained in air-cooled Mo-added steel led to better impact toughness (28J) in comparison with the base steel (23J). Moreover, Mo-added steel possessed higher hardness (291HV), yield (524MPa) and tensile (1108MPa) strengths compared to the base one.
M. Divandari, M. Mehrabian,
Volume 14, Issue 3 (9-2017)
Abstract
This paper investigates the difference between thickness of zinc-based alloys oxide films in dynamic condition using the oxide-metal-oxide (OMO) sandwich method and static condition by theoretical calculations. In dynamic condition, the thickness of the oxide film in the OMO sandwich sample was characterized by scanning electron microscopy (SEM). In the static condition, the thickness and type of the oxide films were studied based on thermodynamic and kinetic estimations. The results showed that the oxide film thickness in molten Zn4Al and ZA27 alloys using OMO sandwich method was estimated to be in the range of 70-200 nm and 30-100 nm, respectively. However, the thickness of oxide films in the static oxidation based on the theoretical calculations, regardless of melt chemical composition, were about 2-5 nm.
N. Nikoogoftar, S. H. Razavi, M. Ghanbari,
Volume 14, Issue 3 (9-2017)
Abstract
In this research, the effect of annealing and aging temperature as well as the effect of quenching media on the microstructure, hardness and dry sliding wear behavior of Ti-6Al-4V alloy has been studied. Cylindrical samples with the diameter of 10 mm and the height of 20mm were solutionized at 930˚C and 1060˚C for 600 seconds and then were quenched in the cold water and in the air. The samples were aged at different temperature of 480˚C, 550˚C and 610˚C for 360 s to increase the hardness. Heat treated samples were tested using standard pin-on-disc test machine at the applied loads of 100, 150 and 200 N. Microstructural investigations using scanning electron microscope revealed that for the samples solutionized at 930˚C and quenched in the water, the microstructure is composed of primary α and high volume fraction of martensitic α΄ phase with fine precipitated of β between martensitic lathes. In the case of air cooled samples, transformed β has also been appeared in the vicinity of primary α. For the samples solutionized at 1060˚C and quenched in the water, fully martensitic micro structure with fine β precipitates was observed. For the sample solutionized at 1060˚C and air quenched, plate like α and lamellar grain boundary β were detected. The maximum hardness value relates to the sample solutionized at 1060˚C and quenched in water which is equal to 433 HV. Different wear mechanisms, including oxidative wear, scratch, and delamination occurred at the worn surfaces at different applied loads. For the samples quenched in the water, the oxidative wear mechanism governing at low applied load and oxide debris was observed as separate or compacted particles which formed in the contact between pin and steel counter face detached from the sample. At higher applied loads, delamination and scratch mechanism was also observed and metallic plate like debris was detached from the sample. Mechanically mixed layer (MML) was formed on the surface of the pin at high applied loads and for the samples with low hardness value adhesion marks were also revealed on the steel disc. The minimum weight loss in the wear test is related to the sample quenched from the 1060ºC in the cold water and aged at 550 ºC .